The East Rockingham Resource Recovery Facility is a $511m energy from waste (EfW) facility located in Rockingham south of Perth. The facility will deliver a vital source of energy and 96% diversion of residual waste from landfill.
What is an Energy Recovery Facility (ERF)?
The new facility, located in the Rockingham Industry Zone 40 kilometres south of Perth, will treat approximately 300,000 tonnes per year of residual waste from municipal, commercial and industrial sources. The EfW plant will generate enough energy to power over 36,000 homes.
The project is supported by a $18m grant from the Australian Renewable Energy Agency (ARENA) and $57.5m subordinated debt from the Clean Energy Finance Corporation (CEFC), alongside a mix of Australian and international lenders. Equity investors include John Laing, Masdar, Hitachi Zosen Innova (HZI) and ACCIONA.
Construction of the facility commenced in early 2020 with full operation expected by the end of 2022.
Veolia’s involvement
Veolia’s role in the facility is as the waste management partner and extends over multiple aspects of the project, including operations and maintenance of the facility, in addition to long-term waste supply.
-
Waste supply – Veolia will supply post-recycling residuals that would otherwise go to landfill.
-
Operations and maintenance – Veolia will lead the delivery of operations and maintenance services for a 20-year term in partnership with Hitachi Zosen Inova (HZI).
-
Disposal services – Veolia will provide best-practice disposal services for fly ash residue and non-processible waste at its North Bannister Resource Recovery Facility.
-
Power offtake – Veolia will purchase reliable renewable electricity generated by the project for its operational requirements across its business in the Perth area.
For more information, visit the dedicated facility webpage here.
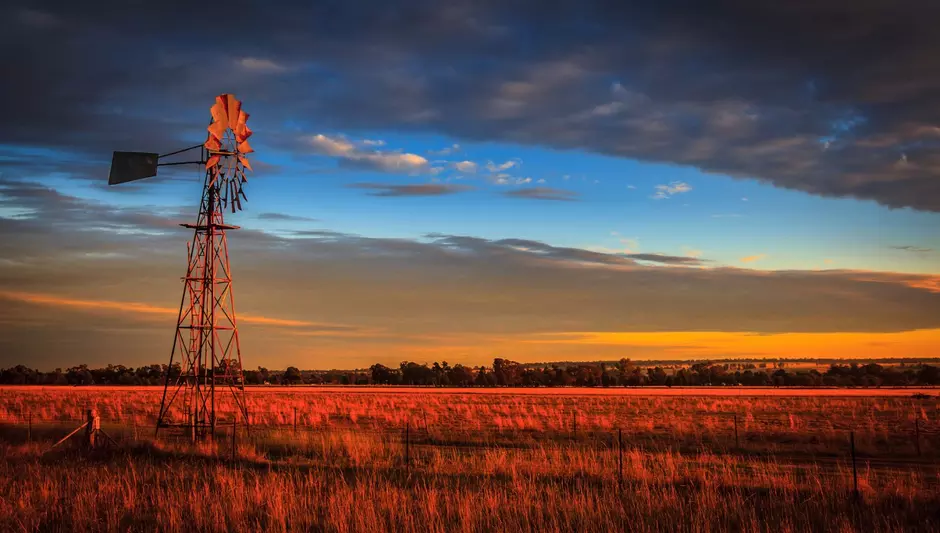
Project Site
The site is located at 26 Office Rd, East Rockingham WA 6168
Get involved
We look forward to sharing more information with you and hearing your views as we continue developing the plant.
We will provide updates on this dedicated project website. If you have a specific question about the project that’s not answered in the FAQs here, please email us at [email protected]. We’ll try to get back to you as soon as possible.
View a video of the project’s progress here:
FAQS
How does energy recovery work?
Waste collection vehicles discharge their waste into a bunker where the waste is mixed to ensure an even burn in the furnace. Water sprays and induction fans are used in the reception hall to reduce levels of dust and smell.
The waste is loaded by crane into a feed hopper, then travels down the feed chute into the furnace.
Inside the furnace, a series of rollers move the waste through the furnace where it is dried and burned at temperatures of around 1000°C.
Burning waste in the furnace creates hot flue gases which travel through a boiler transferring heat to water that runs through the boiler pipes.
The hot water creates steam. The steam drives a turbine which then generates electricity.
Ash created by burning the waste drops into a quench tank, then along a conveyor. Ferrous and non ferrous metals are separated within the ash treatment plant and the remaining product can be used in the construction industry.
The gases from the burned waste are thoroughly cleaned to neutralise acid gases and remove dioxins and heavy metals. The gases are then passed through a fine fabric filter to capture particles before being released through a chimney, which is continuously monitored.
Is it safe?
Yes. Energy recovery technology is a proven and safe technology that is already used by countries extensively across Europe and the UK. The technology is also approved for use in Australia and continues to grow here. The Environmental Impact Assessment for the project will include an independent human health risk assessment. The assessment will consider risks presented to humans from any exposure (inhalation, ingestion, skin contact) to pollutants relevant to the project. The report will be available to the community.
How will emissions be managed?
The plant is being designed and constructed following guidelines set out in the EU Industrial Emissions Directive. These are the highest international standards for air quality. Emissions management is the key to the successful operation of an energy recovery facility, and in fact two-thirds of the footprint of a plant is dedicated to emissions control.
The plant would be equipped with sophisticated 24-hour a day monitoring and fully automated treatment processes to ensure these high standards are met.
An important step to ensuring that emissions meet regulatory standards is the strict control of the fuel used. During fuel preparation, the waste is sorted, inspected, monitored and then processed to remove any hazardous, non-compliant materials which ensures that emissions standards will be met.
In Europe, these energy recovery facilities are built in the middle of major cities and are regularly constructed in built up residential neighbourhoods.
Veolia brings global expertise in developing energy recovery facilities, and has an exceptional track record of building, operating and maintaining energy projects across the world.
Will the plant be noisy?
We understand noise is a concern for the local community and a noise study will be undertaken when looking at potential environmental impacts. We will share results with the community and work through the plant design to minimise noise and ensure that approval and operating conditions can be met.
An example of design considerations is that the fuel would be received in a completely enclosed hall and noise limiting materials will be incorporated into the building design to limit background equipment noises. Development approval conditions apply to the construction and operation of the project.
There will be specific noise management, monitoring and mitigation requirements throughout the whole project.
Will the plant pollute the air?
Emissions from the stack will not adversely effect air quality that occurs in a typical urban environment. The proposed plant will use world’s best available technology to clean, measure and monitor air emissions. Air emissions from the plant will include steam, oxygen, nitrogen and carbon dioxide, all which exist in the atmosphere naturally. Before being released out of the stack, these compounds go through a multi-stage cleaning process to make sure they are neutralised.
Is cogeneration and energy recovery technology used in Australia and elsewhere?
The Boral Cement Works at Berrima in the Southern Highlands uses similar fuel feedstock for cement production works and Visy operates a similar plant in Tumut, NSW.
There are hundreds of energy recovery facilities across the UK, greater Europe, the US and Japan. These countries would not have met their European Union waste recovery and landfill diversion targets without significant investment in energy recovery technology.
In Europe, these energy recovery facilities are built in the middle of major cities, such as Paris, London, Copenhagen and Monaco and are regularly constructed to provide heat energy to adjacent residential neighbourhoods.